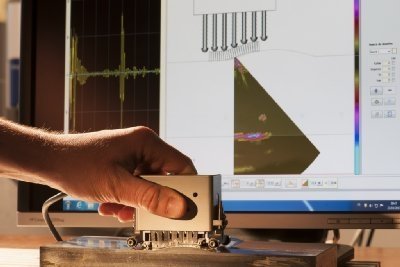
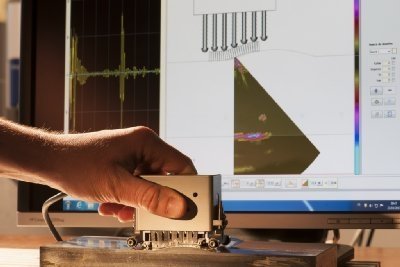
Applications
Contact inspection of parts with irregular geometry : Welds, bends, pipe repairs in nuclear power stations, etc…
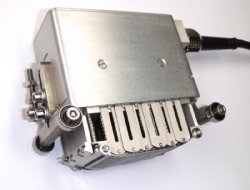
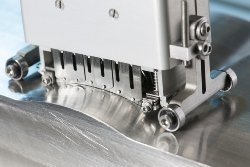
Principle
1D phased array transducers are flexible, and can thus ensure good coupling on the geometry of the inspected part.
The active part consists of a set of independent, articulated mechanical elements, for adapting the geometry in the scanning direction.
The sensor integrates real-time measurement of each element’s position, and thus of the surface, so when it is used with compatible electronics, the delay laws can be adapted in real time to steer the beam by compensating for the variations of the interface.
Advantages
- Feasibility of certain inspections
- Improvement in focusing quality by being freed from the interface geometry
- Increase in lateral resolution through the use of larger active dimensions
Configurations already developped*
Freq. (Mhz)
|
Number of elements
|
Pitch (mm)
|
Total operture (mm)
|
1.5
|
24
|
1.7 x 22
|
41 x 22
|
2
|
24
|
1.4 x 17
|
34 x 17
|
2
|
32
|
1.4 x 17
|
45 x 17
|
4
|
24
|
0.9 x 9
|
22 x 9
|
*These configurations have been developed and tested in the context of given applications. This list is not exhaustive, and the concepts of 1D flexible transducers remain adaptable to the needs of other applications.
Patented Concept
The concept implemented in these transducers, of updating the delay laws in real time according to the real position of individual elements, is covered by a patent registered with the CEA (Atomic Energy Commission, France).
IMASONIC holds the exclusive licence for the use of this patent in designing and manufacturing these transducers.
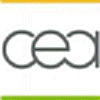